Podcast: Play in new window | Download | Embed
“A lifetime of healthiness achieved through housing” is the mission statement of Phoenix Haus.
I’ve interviewed other Passive House builders using prefabrication in the past, such as Collective Carpentry in episode 149. I’m excited by the possibilities of this approach to provide high quality houses and I’m wondering what it would take to get a company like this started here in New Zealand. (Australia already has Carbonlite!)
Bill McDonald got his start in building by retrofitting old houses to make them more energy efficient. His retrofitting work included airtightness testing, insulation upgrades and replacing windows. And it was through this work that Bill discovered Passive House.
Phoenix Haus
Bill says that the traditional ‘onsite’ construction methodology of the building industry is plagued with inefficiencies. With his entrepreneurial mindset, Bill could see the business benefits of component-based, modular construction for producing high performance houses.
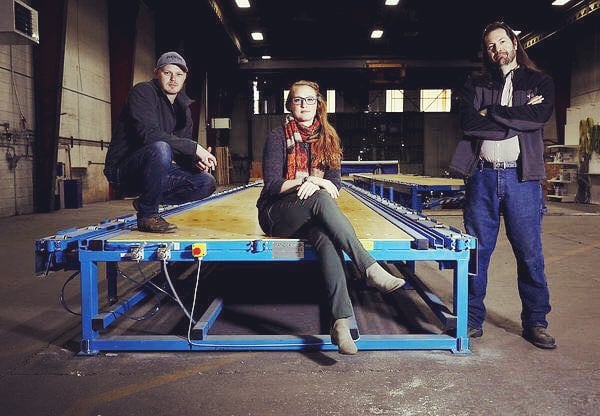
Bill started working for a builder when he was still as high school. He went on to complete a Bachelor of Science in Commercial Real Estate and Finance. After leaving college he continued his education, becoming a Certified Passive House Consultant.
When Bill was working on retrofitting houses, he wanted to present his clients with accurate information about the relative benefits of different options. He would create energy reports based on a computer model, but this process has some big problems. Bill was often not very confident about the numbers he was presenting.
Phoenix Haus and Passive House
The Passive House Planning Package (PHPP) attracted Bill towards learning more about, and ultimately embracing Passive House. He had tried a handful of different energy modelling programmes and would routinely encounter variances of up to 40% in the energy model outputs. When Bill tried PHPP, he was impressed by the accuracy of the model, and the fact that the software took into account everything he believed to be important.
PHPP takes materials and material properties into account. It considers the exact design and location as well as the post-occupancy use.
From Retrofitting to Building New
Bill realised that only so much was possible, or at least viable, when upgrading existing homes. To make really energy efficient, healthy homes, he needed to start from scratch. That’s when Bill started to develop his interest in building new homes.
Health and comfort is a key driver for Phoenix Haus customers. The energy and cost savings are an extra benefit, says Bill.
The Austria House
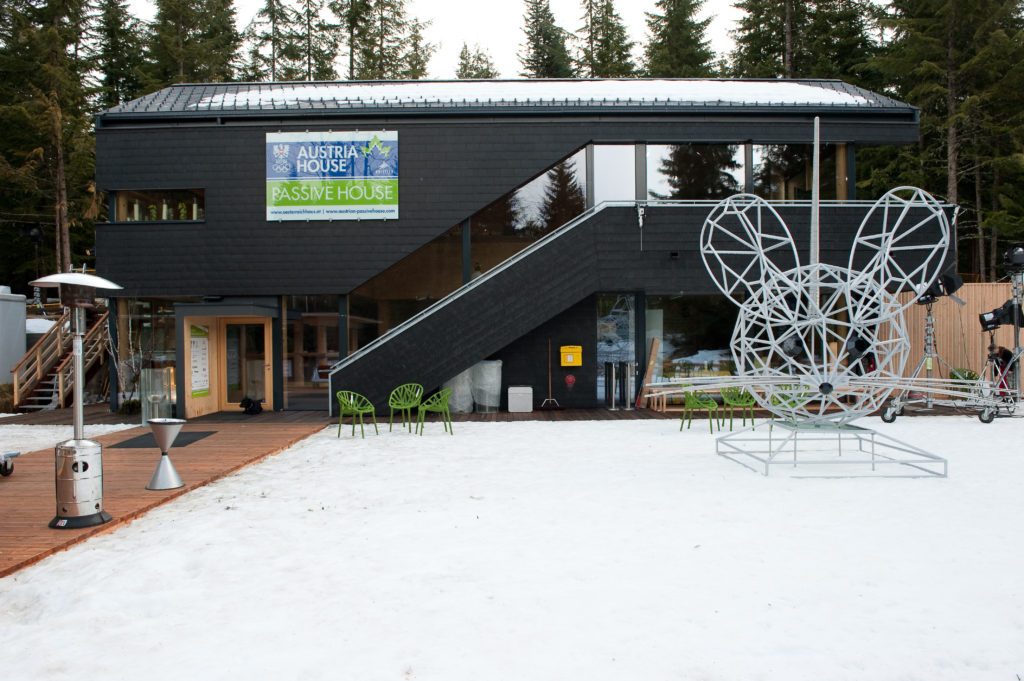
Bill was inspired by Canada’s first Certified Passive House, the ‘Austria Haus‘, now known as Lost Lake Passive House.
Prefab Passive House
Bill worked with Stefan Schneider to transform a stick framed house design into prefabricated Passive House. Check out CutMyTimber’s great photo showcases of projects they’ve progressed from standard design to prefabricated panel construction. Stefan has experience from Europe of this type of construction his collaboration with Bill has influenced the direction of Phoenix Haus.
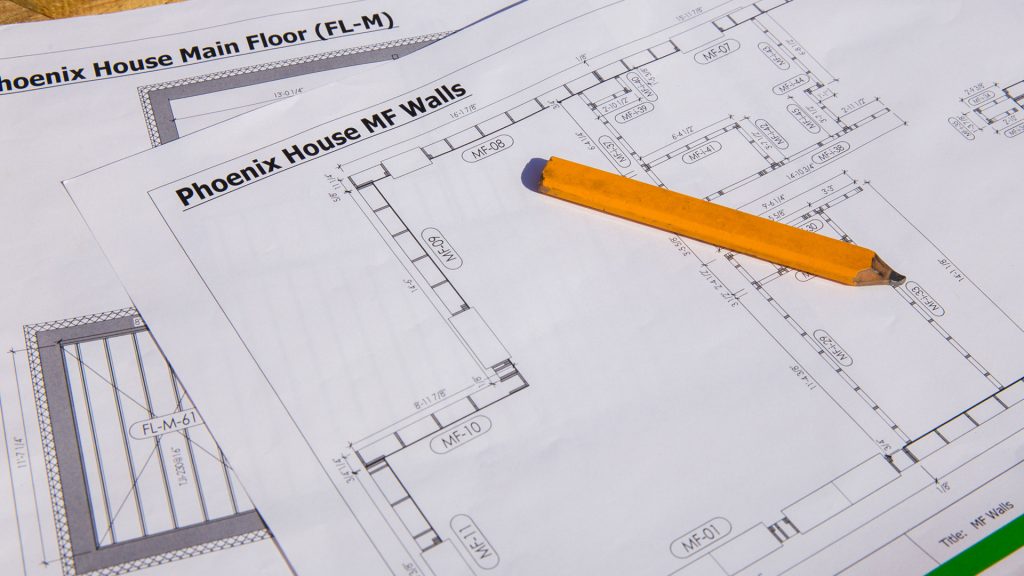
Transitioning from Tradition
Part of the Pheonix Haus growth strategy has been to focus on Passive House as a niche market. Bill mentions the importance of having a solid plan, and then working hard towards that goal. Focusing on Passive House has allowed Bill and his team to leverage the opportunities in a niche market where discerning clients are willing to invest slightly more. These clients appreciate the benefits of high quality construction.
Setting up Shop
Pheonix Haus built their first prototype in rented warehouse with no equipment of their own. They outsourced some of the machining which was done using Hundegger equipment. A contact then suggested that Bill look into Randek who supply specialist prefabrication equipment, such as butterfly tables and full offsite manufacturing assembly lines.
Setting up a factory has been a significant, but calculated investment for Phoenix Haus which is now paying off.
Working with Authorities
Bill also discusses the importance of working with local authorities to educate building control officers that house components can be manufactured offsite. This can often mean dealing with building authorities in different jurisdictions because they manufacture in Colorado, but the building site could be anywhere in North America.
What would it take..?
Some have tried locally, and some are even succeeding here in New Zealand. It’s great to see examples like Ecopanel for example. I understand there are barriers to small-scale, prefabrication of high performance homes in New Zealand, but I still wonder what it would take to start a company like Phoenix Haus in Auckland.
Leave a Reply